Calibração de Equipamentos: A Importância e Os Principais Métodos
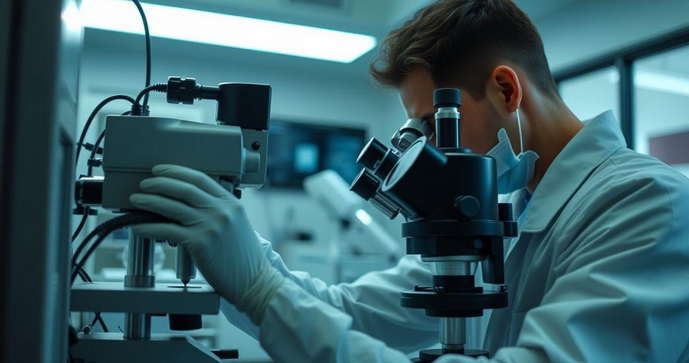
Por: Cláudio - 24 de Maio de 2025
O que é Calibração de Equipamentos e sua Importância
A calibração de equipamentos refere-se ao processo de ajuste e verificação das medições dos instrumentos, a fim de garantir que estejam dentro das especificações exigidas e em conformidade com padrões reconhecidos. Este procedimento é essencial em diversos setores, como industrial, médico e laboratorial, onde a precisão é fundamental para a qualidade e segurança dos produtos e serviços oferecidos.
Um equipamento calibrado garante que as medições realizadas sejam confiáveis e que os resultados obtidos sejam consistentes. Isso é especialmente importante em ambientes onde pequenas variações podem levar a consequências significativas, como em laboratórios de análises químicas ou em processos de produção. A calibração permite que os profissionais identifiquem e corrijam desvios que possam comprometer a eficácia dos processos.
Além disso, a calibração regular dos equipamentos aumenta a vida útil dos instrumentos, prevenindo desgastes prematuros e assegurando que continuem funcionando de acordo com seus parâmetros ideais. A falta de calibração pode resultar em medições imprecisas, comprometendo a qualidade do produto final e colocando em risco a segurança do usuário e do ambiente de trabalho.
Em resumo, a calibração de equipamentos é um processo crucial que não apenas assegura a precisão das medições, mas também contribui para a eficiência e a segurança operacional. Implementar um programa de calibração regular é uma prática recomendada que traz benefícios tangíveis em termos de qualidade e confiabilidade.
Tipos de Equipamentos que Necessitam de Calibração
A calibração é um procedimento essencial para diversos tipos de equipamentos utilizados em diferentes setores. Cada instrumento exige calibração específica para garantir a precisão e a confiabilidade das medições.
A seguir, apresentamos alguns dos principais tipos de equipamentos que necessitam de calibração:
- Instrumentos de Medição de Pressão: Manômetros e transdutores de pressão são frequentemente utilizados em indústrias químicas e petroquímicas. A calibração desses instrumentos é crucial para garantir que as leituras de pressão sejam exatas, evitando falhas no sistema.
- Termômetros: Utilizados em laboratórios e na indústria alimentícia, os termômetros devem ser calibrados para assegurar que as temperaturas medidas estejam corretas, o que é vital para a segurança alimentar e um bom controle de processos.
- Balancas: Em setores como o comércio e a fabricação, balanças devem ser calibradas para garantir que o peso dos produtos esteja correto. A precisão na pesagem é fundamental para manter a conformidade com normas regulatórias e garantir a satisfação do cliente.
- Equipamentos de Teste Elétrico: Multímetros e osciloscópios, usados para medir voltagem, corrente e resistência, necessitam de calibração regular para garantir que as leituras elétricas sejam precisas, evitando problemas em circuitos eletrônicos.
- Equipamentos de Laboratório: Analisadores de gases e espectrômetros requerem calibração constante para assegurar precisão em medições analíticas, que são fundamentais para aplicações científicas e de pesquisa.
- Máquinas de Ensaios: Equipamentos utilizados para testar a resistência e durabilidade de materiais precisam ser calibrados para fornecer resultados confiáveis, assegurando a qualidade dos produtos finais.
Calibrar esses dispositivos não apenas ajuda a garantir a precisão, mas também é um requisito de conformidade para muitas normas e regulamentos do setor. Mantendo os equipamentos calibrados, as empresas conseguem aumentar a eficiência operacional e minimizar riscos.
Processo de Calibração: Passo a Passo
O processo de calibração consiste em uma série de etapas sistemáticas que asseguram que um equipamento mede com precisão.
Seguir um procedimento detalhado aumenta a confiabilidade dos resultados.
A seguir, apresentamos um passo a passo do processo de calibração:
- Preparação do Equipamento: Antes de iniciar a calibração, certifique-se de que o equipamento está limpo e em boas condições de funcionamento.
Verifique todos os componentes e conectores, e limpe eventuais sujeiras que possam interferir nas medições. - Escolha do Padrão de Referência: Selecione um padrão ou equipamento de referência que seja rastreável a um órgão de metrologia nacional.
O padrão deve ser mais preciso do que o equipamento a ser calibrado, pois será utilizado como base para as comparações. - Configuração Inicial: Ligue o equipamento que será calibrado e deixe-o estabilizar conforme as instruções do fabricante.
Este passo é essencial para garantir que o instrumento alcance seu estado ideal de operação. - Execução das Medições: Realize medições utilizando o padrão de referência.
Compare os resultados do equipamento com o padrão e registre os dados.
Para uma calibração mais precisa, é recomendável realizar múltiplas medições. - Ajuste do Equipamento: Se as medições estiverem fora dos limites aceitáveis, é necessário ajustar o equipamento.
Muitos instrumentos contam com ajustes que podem ser feitos de acordo com as instruções do fabricante. - Documentação: Após a calibração, registre todos os resultados, ajustes realizados e dados dos padrões utilizados.
Essa documentação é fundamental para auditorias e rastreabilidade, além de comprovar a precisão do equipamento ao longo do tempo. - Reavaliação Regular: Estabeleça um cronograma para calibrações futuras com base no uso do equipamento e nas recomendações do fabricante.
A reavaliação contribui para a manutenção da precisão das medições.
Seguir essas etapas torna o processo de calibração eficiente e efetivo, garantindo que o equipamento opere dentro dos parâmetros exigidos.
A calibração regular e sistemática é uma prática recomendada que ajuda a prevenir erros, aumentar a qualidade do trabalho e a segurança nas operações.
Intervalos Recomendados para Calibração
Determinar a frequência adequada para a calibração de equipamentos é fundamental para garantir medições precisas e confiáveis.
O intervalo recomendado para calibração pode variar dependendo de vários fatores, incluindo o tipo de equipamento, a frequência de uso e as condições ambientais.
A seguir, apresentamos algumas diretrizes gerais sobre os intervalos de calibração:
- Equipamentos de Medição Crítica: Para instrumentos que têm impacto direto na segurança ou na qualidade do produto, como em laboratórios de análises químicas ou indústrias farmacêuticas, a calibração deve ser realizada com frequência, normalmente a cada seis meses.
- Equipamentos de Uso Regular: Instrumentos que são utilizados diariamente, como balanças em ambientes comerciais, devem ser calibrados uma vez por ano, garantindo que permaneçam dentro dos padrões de precisão requeridos.
- Equipamentos de Uso Ocasional: Se o equipamento é utilizado raramente ou em aplicações menos críticas, como alguns aparelhos de medição em jardinagem, a calibração pode ser feita a cada 2 anos, desde que sua precisão seja verificada regularmente antes do uso.
- Condições Ambientais: Em ambientes com alta variação de temperatura, umidade ou outras condições adversas, a calibração deve ser feita com mais frequência.
Essas variáveis podem afetar o desempenho dos equipamentos, exigindo uma maior atenção. - Após Transporte ou Manutenção: Sempre que um equipamento passar por transporte, reparos ou manutenção significativa, ele deve ser recalibrado.
Isso assegura que qualquer impacto físico ou alteração feita durante o processo não afete sua precisão. - Normas Regulamentares: É importante estar ciente das normas e regulamentações específicas do setor em que se opera.
Muitas vezes, essas normas estipulam os intervalos de calibração recomendados a serem seguidos.
Mantendo um calendário rigoroso de calibrações, as empresas podem garantir a precisão contínua de suas medições, aumentar a confiança dos clientes e evitar custos associados a erros de medição.
A implementação de práticas regulares de calibração deve ser vista como um investimento em qualidade e eficiência operacionais.
Erro de Medição e Como Evitá-lo
O erro de medição é uma ocorrência comum que pode afetar a precisão e confiabilidade dos resultados obtidos por equipamentos.
Esses erros podem surgir de diversos fatores, e sua mitigação é fundamental para garantir medições corretas e consistentes.
A seguir, estão os principais tipos de erros de medição e algumas estratégias para evitá-los:
- Erros Sistemáticos: Esses erros ocorrem devido a falhas constantes no sistema de medição, como problemas de calibração ou desvios em relação ao padrão.
Para evitá-los, é crucial realizar calibrações regulares e manter registros detalhados dos resultados.
A verificação de padrões de referência também ajuda a identificar e corrigir erros sistemáticos. - Erros Aleatórios: Resultantes de flutuações imprevisíveis nas medições, esses erros podem ser minimizados através da repetição de medições.
Realizar múltiplas medições e calcular a média ajuda a suavizar variações inesperadas e proporciona um resultado mais confiável. - Erros de Parâmetros Ambientais: Variações na temperatura, pressão e umidade podem impactar a precisão dos instrumentos.
Para evitar esses erros, recomenda-se a utilização de instrumentos em ambientes controlados e a consideração das condições ambientais ao interpretar os resultados. - Erros Humanos: Muitas vezes, erros na operação do equipamento podem ocorrer devido à falta de treinamento ou atenção.
Proporcionar formação adequada aos operadores e implementar procedimentos de verificação antes da medição pode ajudar a reduzir erros humanos. - Erros de Instalação: Equipamentos mal instalados podem levar a medições imprecisas.
Para minimizar esses erros, siga as instruções do fabricante para a instalação, garantindo que todos os componentes estejam corretamente posicionados e alinhados. - Uso de Equipamentos Inadequados: A utilização de instrumentos que não são apropriados para a tarefa em questão pode resultar em erros de medição.
Sempre escolha o equipamento correto para cada tipo de medição, levando em consideração fatores como faixa de medição e especificações técnicas.
Ao identificar e entender os tipos de erros de medição, as empresas podem implementar medidas proativas para evitá-los, garantindo resultados mais precisos e confiáveis.
A constante melhoria nos processos de medição contribui diretamente para a qualidade operacional e a satisfação do cliente.
Normas e Padrões para Calibração de Equipamentos
As normas e padrões para calibração de equipamentos desempenham um papel crucial na garantia da precisão e confiabilidade nas medições. Elas são estabelecidas por organizações reconhecidas e visam proporcionar critérios claros e consistentes para a calibração de diversos tipos de instrumentos em diferentes setores.
A seguir, discutimos algumas das principais normas e padrões associados à calibração:
- ISO 9001: Esta norma define requisitos para um sistema de gestão da qualidade, assegurando que os processos estejam sob controle e que a calibração dos equipamentos seja realizada com regularidade para atender às especificações do cliente.
- ISO/IEC 17025: Esta norma é específica para laboratórios de ensaio e calibração, estabelecendo requisitos para a competência técnica e a gestão de qualidade. É reconhecida internacionalmente e garante que os laboratórios realizem calibrações precisas de acordo com procedimentos padronizados.
- GUM (Guide to the Expression of Uncertainty in Measurement): Este guia fornece diretrizes sobre como expressar incertezas de medição, fundamental para a calibração, pois ajuda a interpretar e comunicar a precisão dos resultados obtidos.
- ASTM International: O ASTM desenvolve normas que tratam de diferentes materiais, produtos e sistemas. Muitas dessas normas incluem diretrizes específicas para a calibração de equipamentos utilizados em ensaios de materiais, garantindo que os resultados sejam comparáveis e confiáveis.
- ANSI/NCSL Z540: Esta norma se concentra na calibração de instrumentos de medição, abordando aspectos de rastreabilidade e verificação. Assegura que os resultados de medição sejam comparáveis a padrões reconhecidos nacionalmente ou internacionalmente.
- Normas Setoriais: Além das normas gerais, muitos setores possuem suas próprias diretrizes específicas. Por exemplo, a indústria farmacêutica pode seguir normas específicas da FDA, enquanto laboratórios de análises químicas seguem diretrizes do ISO 17025.
Seguir normas e padrões bem estabelecidos para calibração é fundamental não apenas para garantir a precisão e a qualidade das medições, mas também para assegurar conformidade com regulamentações e aumento da credibilidade junto a clientes e parceiros.
A constante atualização e aderência a essas normas permitem que as organizações mantenham altos níveis operacionais e de satisfação do cliente.
A calibração de equipamentos é um processo essencial que assegura a precisão e a confiabilidade das medições em diversos setores. Compreender os conceitos envolvidos, incluindo os tipos de equipamentos que necessitam de calibração, o processo que deve ser seguido, os intervalos recomendados, os erros que podem ocorrer e as normas relevantes, é fundamental para qualquer organização que busca manter altos padrões de qualidade.
Implementar um programa de calibração robusto não apenas melhora a precisão das medições, mas também contribui para a eficiência operacional e a segurança. Ao aderir às boas práticas e normas reconhecidas, as empresas garantem a conformidade e a satisfação do cliente. Por isso, investir na calibração adequada é um passo decisivo para assegurar a qualidade e a confiabilidade dos produtos e serviços oferecidos.