Calibração de Equipamentos: Como Garantir Precisão e Confiabilidade em Seus Instrumentos
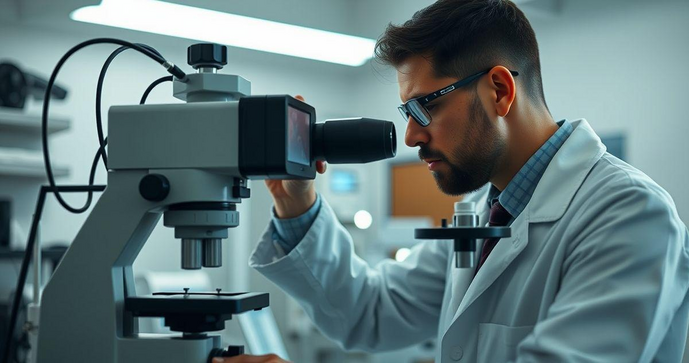
Por: Cláudio - 18 de Abril de 2025
A calibração de equipamentos é um processo fundamental para garantir a precisão e a confiabilidade das medições em diversas áreas, como indústria, laboratórios e serviços técnicos. Com o avanço da tecnologia, a necessidade de manter instrumentos calibrados se torna cada vez mais evidente, pois resultados imprecisos podem levar a erros significativos e prejuízos. Neste artigo, abordaremos a importância da calibração, os passos necessários para realizá-la corretamente e os cuidados que devem ser tomados para evitar erros comuns.
Importância da Calibração de Equipamentos para a Precisão
A calibração de equipamentos é um procedimento essencial que assegura a precisão e a confiabilidade das medições realizadas por instrumentos de medição. Em um mundo onde a exatidão é crucial, a calibração se torna uma prática indispensável em diversas indústrias, incluindo farmacêutica, alimentícia, química e de manufatura. A seguir, discutiremos a importância da calibração de equipamentos e como ela impacta a qualidade dos resultados obtidos.
Um dos principais motivos para a calibração de equipamentos é garantir que as medições estejam dentro das especificações estabelecidas. Instrumentos de medição, como balanças, termômetros e manômetros, podem sofrer desgastes ao longo do tempo, resultando em leituras imprecisas. Quando um equipamento não está calibrado corretamente, os dados coletados podem levar a decisões erradas, comprometendo a qualidade do produto final e a segurança dos processos. Por exemplo, na indústria alimentícia, uma balança descalibrada pode resultar em porções incorretas, afetando a consistência e a segurança dos alimentos.
Além disso, a calibração de equipamentos é fundamental para atender a normas e regulamentações. Muitas indústrias são obrigadas a seguir padrões específicos de qualidade, que incluem a calibração regular de seus instrumentos. A conformidade com essas normas não apenas garante a qualidade dos produtos, mas também protege a empresa de possíveis sanções legais e prejuízos financeiros. Por exemplo, laboratórios que realizam testes de controle de qualidade devem garantir que seus equipamentos estejam calibrados para fornecer resultados válidos e confiáveis.
A calibração também desempenha um papel crucial na manutenção da reputação da empresa. A confiança dos clientes é um ativo valioso, e a entrega de produtos e serviços de alta qualidade é fundamental para manter essa confiança. Quando uma empresa demonstra compromisso com a precisão e a qualidade, ela se destaca no mercado e conquista a lealdade dos clientes. Por outro lado, falhas em medições podem resultar em produtos defeituosos, recalls e danos à imagem da marca.
Outro aspecto importante da calibração é a redução de custos a longo prazo. Embora a calibração possa envolver um investimento inicial, a precisão nos processos pode levar a economias significativas. Equipamentos calibrados corretamente operam de maneira mais eficiente, reduzindo o desperdício de materiais e minimizando retrabalhos. Além disso, a detecção precoce de problemas em equipamentos pode evitar falhas catastróficas que exigiriam reparos dispendiosos ou a substituição do equipamento.
É importante ressaltar que a calibração não é um evento único, mas sim um processo contínuo. A frequência com que os equipamentos devem ser calibrados depende de vários fatores, incluindo o tipo de equipamento, a intensidade de uso e as condições ambientais. Por exemplo, equipamentos que são utilizados em ambientes agressivos ou que passam por ciclos de uso intensivo podem exigir calibrações mais frequentes. Portanto, é essencial estabelecer um cronograma de calibração que atenda às necessidades específicas de cada equipamento.
Além disso, a calibração deve ser realizada por profissionais qualificados e em laboratórios acreditados. A utilização de padrões de referência rastreáveis é fundamental para garantir a precisão das medições. A calibração de balanças, por exemplo, deve ser realizada por técnicos especializados que utilizam pesos padrão certificados para garantir a exatidão das leituras. Para mais informações sobre esse processo, você pode conferir a Calibração de balanças e entender como garantir a precisão em suas medições.
Em resumo, a calibração de equipamentos é um componente vital para garantir a precisão e a confiabilidade das medições em diversas indústrias. A prática não apenas assegura a conformidade com normas e regulamentações, mas também protege a reputação da empresa e contribui para a redução de custos. Portanto, investir em calibração regular é uma decisão estratégica que pode trazer benefícios significativos a longo prazo. Ao priorizar a calibração, as empresas podem garantir a qualidade de seus produtos e serviços, promovendo a confiança e a satisfação dos clientes.
Passo a Passo para Realizar a Calibração de Equipamentos
A calibração de equipamentos é um processo essencial para garantir a precisão e a confiabilidade das medições. Realizar a calibração de forma adequada envolve uma série de etapas que devem ser seguidas rigorosamente. Abaixo, apresentamos um guia passo a passo para realizar a calibração de equipamentos, assegurando que você obtenha resultados precisos e confiáveis.
1. Preparação do Equipamento
Antes de iniciar o processo de calibração, é fundamental preparar o equipamento. Isso inclui a limpeza do instrumento e a verificação de seu estado geral. Certifique-se de que não há sujeira, poeira ou resíduos que possam interferir nas medições. Além disso, verifique se todas as partes móveis estão funcionando corretamente e se não há sinais de desgaste ou danos. Se o equipamento estiver em más condições, pode ser necessário realizar reparos antes da calibração.
2. Reunir os Materiais Necessários
Para realizar a calibração, você precisará de materiais adequados, como padrões de referência, pesos calibrados ou dispositivos de medição que sejam rastreáveis a padrões nacionais ou internacionais. É importante que esses padrões sejam certificados e estejam dentro do intervalo de medição do equipamento que está sendo calibrado. Por exemplo, ao realizar a Calibração de torquímetro, você deve utilizar pesos que correspondam às especificações do torquímetro em questão.
3. Estabelecer as Condições Ambientais
As condições ambientais podem afetar a precisão das medições. Portanto, é importante realizar a calibração em um ambiente controlado, onde a temperatura, umidade e pressão atmosférica sejam mantidas dentro de limites aceitáveis. Verifique se o local de calibração está livre de vibrações, correntes de ar e outras interferências que possam impactar os resultados. Se necessário, utilize equipamentos de climatização para garantir um ambiente estável.
4. Realizar a Calibração
Com o equipamento preparado e os materiais prontos, você pode iniciar o processo de calibração. Siga as instruções do fabricante para o equipamento específico que está sendo calibrado. Isso pode incluir a realização de medições em diferentes pontos do intervalo de operação do equipamento. Registre os valores obtidos e compare-os com os padrões de referência. Se as medições estiverem fora dos limites aceitáveis, ajustes devem ser feitos no equipamento.
5. Ajustes e Correções
Se durante a calibração você identificar que o equipamento não está dentro das especificações, será necessário realizar ajustes. Isso pode envolver a alteração de configurações, a substituição de peças ou a reprogramação do dispositivo. Após realizar os ajustes, repita o processo de calibração para garantir que o equipamento agora esteja operando corretamente. É importante documentar todos os ajustes realizados, pois isso pode ser útil para futuras manutenções e calibrações.
6. Documentação dos Resultados
Após concluir a calibração, é essencial documentar todos os resultados obtidos. Isso inclui as medições iniciais, os ajustes realizados e as medições finais. A documentação deve ser clara e detalhada, permitindo que outros profissionais possam entender o processo realizado. Além disso, mantenha registros de calibrações anteriores, pois isso pode ajudar a identificar padrões de desempenho e a necessidade de manutenção futura.
7. Estabelecer um Cronograma de Calibração
A calibração não deve ser vista como um evento isolado, mas sim como parte de um programa contínuo de manutenção. Estabeleça um cronograma de calibração regular com base nas recomendações do fabricante e nas necessidades específicas do seu equipamento. A frequência da calibração pode variar dependendo do uso, das condições ambientais e da criticidade das medições. Um cronograma bem definido ajuda a garantir que todos os equipamentos permaneçam dentro das especificações e operem de forma confiável.
8. Treinamento e Capacitação
Por fim, é importante garantir que os profissionais responsáveis pela calibração estejam devidamente treinados e capacitados. O conhecimento sobre os procedimentos corretos de calibração, bem como a compreensão das especificações do equipamento, são fundamentais para obter resultados precisos. Considere a realização de treinamentos regulares e a atualização de conhecimentos para manter a equipe preparada para lidar com as demandas de calibração.
Seguir este passo a passo para a calibração de equipamentos não apenas assegura a precisão das medições, mas também contribui para a qualidade e a segurança dos processos. A calibração adequada é um investimento que traz benefícios significativos a longo prazo, garantindo que os equipamentos operem de maneira eficiente e confiável.
Erros Comuns na Calibração e Como Evitá-los
A calibração de equipamentos é um processo crítico que garante a precisão e a confiabilidade das medições. No entanto, existem diversos erros que podem ocorrer durante esse processo, comprometendo os resultados e a eficácia do equipamento. Neste artigo, abordaremos os erros comuns na calibração e forneceremos dicas sobre como evitá-los, assegurando que você obtenha medições precisas e confiáveis.
1. Falta de Preparação Adequada
Um dos erros mais frequentes na calibração é a falta de preparação adequada do equipamento. Antes de iniciar o processo, é essencial garantir que o instrumento esteja limpo e em boas condições de funcionamento. A sujeira, poeira ou resíduos podem interferir nas medições, levando a resultados imprecisos. Para evitar esse erro, sempre realize uma inspeção visual do equipamento e faça a limpeza necessária antes de iniciar a calibração.
2. Uso de Padrões de Referência Inadequados
Outro erro comum é a utilização de padrões de referência que não são adequados ou que não estão devidamente certificados. Os padrões de referência devem ser rastreáveis a padrões nacionais ou internacionais e devem estar dentro do intervalo de medição do equipamento que está sendo calibrado. Usar padrões inadequados pode resultar em medições erradas e comprometer a precisão do equipamento. Para evitar esse erro, sempre verifique a certificação e a adequação dos padrões de referência que você está utilizando.
3. Ignorar as Condições Ambientais
As condições ambientais podem ter um impacto significativo nas medições. Ignorar fatores como temperatura, umidade e pressão atmosférica pode levar a resultados imprecisos. Por exemplo, se a calibração for realizada em um ambiente com variações extremas de temperatura, isso pode afetar o desempenho do equipamento. Para evitar esse erro, sempre realize a calibração em um ambiente controlado, onde as condições sejam mantidas dentro de limites aceitáveis.
4. Não Realizar Ajustes Necessários
Após a calibração, é comum que os técnicos não realizem os ajustes necessários no equipamento, mesmo quando as medições estão fora das especificações. Ignorar a necessidade de ajustes pode resultar em medições imprecisas e comprometer a qualidade do produto final. Para evitar esse erro, sempre documente os resultados da calibração e faça os ajustes necessários antes de finalizar o processo. Isso garantirá que o equipamento esteja operando dentro das especificações.
5. Falta de Documentação Adequada
A documentação é uma parte crucial do processo de calibração. A falta de registros detalhados pode levar a confusões e erros em calibrações futuras. É importante documentar todos os resultados obtidos, os ajustes realizados e as condições em que a calibração foi realizada. Para evitar esse erro, estabeleça um sistema de documentação claro e consistente, que permita que outros profissionais compreendam o processo realizado e os resultados obtidos.
6. Não Seguir as Instruções do Fabricante
Cada equipamento possui especificações e procedimentos de calibração únicos, que devem ser seguidos rigorosamente. Ignorar as instruções do fabricante pode resultar em medições imprecisas e até mesmo danos ao equipamento. Para evitar esse erro, sempre consulte o manual do fabricante e siga as diretrizes específicas para a calibração do seu equipamento. Isso garantirá que você esteja realizando o processo corretamente e obtendo resultados confiáveis.
7. Falta de Treinamento e Capacitação
A calibração deve ser realizada por profissionais qualificados e treinados. A falta de conhecimento sobre os procedimentos corretos pode levar a erros significativos. Para evitar esse erro, invista em treinamentos regulares para sua equipe, garantindo que todos estejam atualizados sobre as melhores práticas de calibração. A capacitação contínua é fundamental para manter a precisão e a confiabilidade das medições.
8. Não Realizar Calibrações Regulares
Um erro comum que pode comprometer a precisão das medições é a falta de um cronograma de calibração regular. A calibração não deve ser vista como um evento isolado, mas sim como parte de um programa contínuo de manutenção. Para evitar esse erro, estabeleça um cronograma de calibração com base nas recomendações do fabricante e nas necessidades específicas do seu equipamento. Isso garantirá que todos os instrumentos permaneçam dentro das especificações e operem de forma confiável.
9. Ignorar a Calibração de Equipamentos Críticos
Alguns equipamentos são mais críticos do que outros e, portanto, exigem atenção especial em relação à calibração. Ignorar a calibração de equipamentos essenciais, como válvulas de segurança, pode resultar em falhas catastróficas. A Calibração de válvula de segurança é um exemplo de como a precisão é vital para a segurança operacional. Para evitar esse erro, identifique quais equipamentos são críticos para suas operações e priorize a calibração regular desses instrumentos.
Em resumo, a calibração de equipamentos é um processo que requer atenção e cuidado. Ao evitar os erros comuns mencionados acima, você pode garantir que suas medições sejam precisas e confiáveis. A implementação de boas práticas de calibração não apenas melhora a qualidade dos produtos e serviços, mas também protege a reputação da sua empresa e contribui para a segurança operacional. Investir tempo e recursos na calibração adequada é um passo essencial para o sucesso a longo prazo.
Frequência Recomendada para a Calibração de Equipamentos
A calibração de equipamentos é um aspecto crucial para garantir a precisão e a confiabilidade das medições em diversas indústrias. No entanto, a eficácia desse processo depende não apenas da execução correta da calibração, mas também da frequência com que ela é realizada. A seguir, discutiremos a importância de estabelecer uma frequência adequada para a calibração de equipamentos e os fatores que influenciam essa decisão.
1. Importância da Frequência de Calibração
Estabelecer uma frequência de calibração adequada é fundamental para garantir que os equipamentos operem dentro das especificações e forneçam medições precisas. A calibração regular ajuda a identificar e corrigir problemas antes que eles se tornem críticos, evitando falhas que podem resultar em prejuízos financeiros, perda de tempo e até riscos à segurança. Além disso, a calibração frequente é essencial para atender a normas e regulamentações que exigem a manutenção de padrões de qualidade.
2. Fatores que Influenciam a Frequência de Calibração
Vários fatores devem ser considerados ao determinar a frequência de calibração de um equipamento. Entre eles, destacam-se:
- Tipo de Equipamento: Diferentes tipos de equipamentos têm diferentes requisitos de calibração. Por exemplo, instrumentos de medição de alta precisão, como balanças analíticas, podem exigir calibrações mais frequentes do que equipamentos menos sensíveis.
- Intensidade de Uso: Equipamentos que são utilizados com frequência ou em condições adversas podem precisar de calibrações mais regulares. O uso intenso pode levar a desgastes mais rápidos e, consequentemente, a desvios nas medições.
- Condições Ambientais: A temperatura, umidade e pressão atmosférica do ambiente onde o equipamento opera podem afetar sua precisão. Equipamentos expostos a condições extremas podem necessitar de calibrações mais frequentes.
- Histórico de Calibração: O histórico de calibração do equipamento também deve ser considerado. Se um instrumento frequentemente apresenta desvios, pode ser necessário aumentar a frequência de calibração para garantir a precisão.
- Normas e Regulamentações: Algumas indústrias são regidas por normas específicas que determinam a frequência mínima de calibração. É importante estar ciente dessas exigências para garantir a conformidade.
3. Recomendações Gerais de Frequência
Embora a frequência de calibração deva ser determinada com base nos fatores mencionados, algumas recomendações gerais podem ser seguidas:
- Equipamentos de Alta Precisão: Para instrumentos de medição de alta precisão, como balanças analíticas e medidores de pressão, recomenda-se a calibração a cada 6 meses a 1 ano.
- Equipamentos de Uso Moderado: Equipamentos que são utilizados com frequência moderada, como termômetros e multímetros, podem ser calibrados anualmente ou a cada 2 anos.
- Equipamentos de Baixa Precisão: Instrumentos que não exigem alta precisão, como ferramentas manuais, podem ser calibrados a cada 2 a 3 anos, dependendo do uso.
4. Estabelecendo um Cronograma de Calibração
Para garantir que todos os equipamentos sejam calibrados de forma adequada e no tempo certo, é importante estabelecer um cronograma de calibração. Esse cronograma deve incluir:
- Uma lista de todos os equipamentos que precisam ser calibrados.
- A frequência recomendada de calibração para cada equipamento.
- As datas programadas para a calibração.
- Os responsáveis pela execução da calibração e pela documentação dos resultados.
Um cronograma bem estruturado ajuda a evitar esquecimentos e garante que todos os equipamentos sejam mantidos dentro das especificações.
5. A Importância de Profissionais Qualificados
Realizar a calibração de equipamentos deve ser feito por profissionais qualificados e experientes. A utilização de uma Empresa de calibração de instrumentos de medição pode garantir que os procedimentos sejam seguidos corretamente e que os resultados sejam confiáveis. Profissionais treinados têm o conhecimento necessário para identificar problemas e realizar ajustes adequados, assegurando que os equipamentos operem com precisão.
6. Revisão e Ajustes no Cronograma
É importante revisar e ajustar o cronograma de calibração periodicamente. À medida que as condições de operação mudam ou novos equipamentos são adquiridos, pode ser necessário reavaliar a frequência de calibração. Além disso, se um equipamento apresentar desvios frequentes, pode ser necessário aumentar a frequência de calibração para garantir a precisão.
7. Conclusão
Estabelecer uma frequência adequada para a calibração de equipamentos é essencial para garantir a precisão e a confiabilidade das medições. Considerar fatores como tipo de equipamento, intensidade de uso e condições ambientais ajudará a determinar a frequência ideal. Além disso, manter um cronograma de calibração e contar com profissionais qualificados são práticas que contribuem para a eficácia do processo. Ao priorizar a calibração regular, as empresas podem garantir a qualidade de seus produtos e serviços, promovendo a confiança e a satisfação dos clientes.
Em resumo, a calibração de equipamentos é uma prática essencial que não pode ser negligenciada em qualquer setor que dependa de medições precisas. A manutenção regular e adequada dos instrumentos não apenas assegura a qualidade dos produtos e serviços, mas também protege a segurança e a integridade dos processos operacionais. Ao seguir as diretrizes apresentadas, como a definição de uma frequência de calibração apropriada e a realização do processo por profissionais qualificados, as empresas podem minimizar riscos e maximizar a eficiência. Portanto, investir na calibração é um passo crucial para garantir resultados confiáveis e manter a competitividade no mercado.