Calibração de manômetros é essencial para garantir precisão e segurança em medições industriais
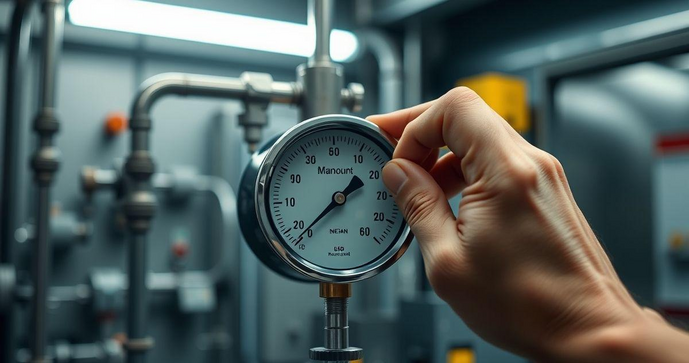
Por: Cláudio - 23 de Maio de 2025
A calibração de manômetros é um processo fundamental para garantir a precisão e a confiabilidade das medições em diversos setores, como industrial e laboratorial. Com o aumento das exigências de qualidade e segurança, a correta calibração desses instrumentos se torna essencial para evitar erros que podem comprometer a integridade de processos e produtos. Neste artigo, abordaremos a importância da calibração de manômetros, os métodos utilizados, a frequência recomendada e os erros comuns que devem ser evitados.
Importância da Calibração de Manômetros na Indústria
A calibração de manômetros é um aspecto crucial na manutenção da precisão e confiabilidade dos instrumentos de medição utilizados em diversos setores industriais. Os manômetros são dispositivos que medem a pressão de gases ou líquidos, e sua precisão é vital para garantir a segurança e a eficiência dos processos. Quando um manômetro não está calibrado corretamente, pode resultar em medições imprecisas, levando a decisões erradas que podem comprometer a qualidade do produto final e a segurança operacional.
Um dos principais motivos para a calibração de manômetros é a necessidade de conformidade com normas e regulamentos. Muitas indústrias, especialmente aquelas que operam em setores regulados, como farmacêutico, alimentício e petroquímico, devem seguir padrões rigorosos de qualidade. A calibração regular dos manômetros é uma exigência para garantir que os instrumentos estejam funcionando dentro das especificações estabelecidas. Isso não apenas ajuda a evitar penalidades legais, mas também assegura que os produtos atendam aos padrões de qualidade exigidos pelo mercado.
Além da conformidade regulatória, a calibração de manômetros é essencial para a segurança dos trabalhadores e do ambiente. Medições imprecisas de pressão podem levar a situações perigosas, como explosões, vazamentos ou falhas em equipamentos. Por exemplo, em uma planta petroquímica, um manômetro que indica uma pressão incorreta pode resultar em uma reação descontrolada, colocando em risco a vida dos operadores e causando danos significativos à instalação. Portanto, a calibração regular é uma prática preventiva que ajuda a mitigar esses riscos.
Outro aspecto importante da calibração de manômetros é a otimização dos processos industriais. A precisão nas medições de pressão é fundamental para o controle de processos, pois permite que os operadores ajustem as condições de operação de maneira eficaz. Por exemplo, em um sistema de bombeamento, a pressão correta deve ser mantida para garantir que o fluido seja transportado de maneira eficiente. Se um manômetro estiver descalibrado, pode resultar em pressão excessiva ou insuficiente, afetando a eficiência do sistema e aumentando os custos operacionais.
Além disso, a calibração de manômetros contribui para a longevidade dos equipamentos. Instrumentos que não são calibrados regularmente podem sofrer desgaste prematuro e falhas, resultando em custos elevados de manutenção e substituição. A calibração ajuda a identificar problemas potenciais antes que se tornem críticos, permitindo que as empresas realizem manutenções preventivas e evitem paradas não programadas. Isso é especialmente importante em ambientes industriais, onde a continuidade das operações é vital para a produtividade.
Outro ponto a ser considerado é a importância da calibração na melhoria da qualidade do produto. Em muitas indústrias, a pressão é um parâmetro crítico que afeta diretamente as características do produto final. Por exemplo, na indústria alimentícia, a pressão de cozimento pode influenciar a textura e o sabor dos alimentos. Se os manômetros não estiverem calibrados corretamente, isso pode resultar em produtos de qualidade inferior, afetando a satisfação do cliente e a reputação da marca. Portanto, a calibração regular é uma prática que não apenas garante a segurança, mas também assegura a qualidade do produto.
Por fim, a calibração de manômetros é uma prática que deve ser integrada à cultura de qualidade de uma organização. As empresas que reconhecem a importância da calibração e investem em processos de medição precisos tendem a ter um desempenho superior em comparação com aquelas que negligenciam essa prática. A calibração deve ser vista como um investimento, e não como um custo, pois os benefícios a longo prazo superam amplamente os gastos associados.
Em resumo, a calibração de manômetros é uma prática essencial na indústria, garantindo a precisão das medições, a conformidade com normas, a segurança dos trabalhadores, a otimização dos processos e a qualidade do produto. Para garantir que seus manômetros estejam sempre em condições ideais de funcionamento, é recomendável realizar a calibração de manômetros regularmente, seguindo as diretrizes e recomendações dos fabricantes. Essa abordagem proativa não apenas protege a integridade dos processos, mas também contribui para a sustentabilidade e o sucesso a longo prazo da operação industrial.
Métodos Comuns de Calibração de Manômetros
A calibração de manômetros é um processo essencial para garantir a precisão e a confiabilidade das medições de pressão em diversos setores industriais. Existem vários métodos de calibração que podem ser utilizados, dependendo do tipo de manômetro, da aplicação e dos recursos disponíveis. Neste artigo, abordaremos os métodos mais comuns de calibração de manômetros, destacando suas características, vantagens e desvantagens.
Um dos métodos mais tradicionais de calibração de manômetros é o uso de um manômetro de referência. Este método envolve a comparação do manômetro a ser calibrado com um manômetro de alta precisão, que serve como padrão. O manômetro de referência é conectado ao mesmo ponto de pressão que o manômetro em teste, e as leituras de ambos os instrumentos são comparadas em diferentes pontos de pressão. Este método é eficaz e amplamente utilizado, pois permite identificar desvios de calibração e ajustar o manômetro conforme necessário.
Outra abordagem comum é a calibração por pressão de gás. Neste método, um sistema de pressão de gás é utilizado para gerar pressões conhecidas, que são aplicadas ao manômetro em teste. O manômetro é então ajustado para corresponder às pressões de referência. Este método é especialmente útil para manômetros que medem pressões de gás, pois permite uma calibração precisa em uma ampla faixa de pressões. No entanto, é importante garantir que o sistema de pressão de gás esteja devidamente calibrado e mantido para garantir resultados precisos.
O método de calibração por pressão de líquido é outra técnica utilizada, especialmente para manômetros que medem a pressão de líquidos. Neste caso, um coluna de líquido é utilizada para gerar pressão, e o manômetro é calibrado em relação a essa pressão. Este método é simples e eficaz, mas pode ser limitado pela densidade do líquido utilizado e pela altura da coluna necessária para gerar a pressão desejada. É importante escolher um líquido adequado que não reaja com os materiais do manômetro.
Além dos métodos mencionados, a calibração eletrônica tem se tornado cada vez mais popular, especialmente com o avanço da tecnologia. Este método utiliza dispositivos eletrônicos para gerar pressões conhecidas e medir a resposta do manômetro. A calibração eletrônica pode ser realizada de forma automatizada, o que aumenta a eficiência e a precisão do processo. Além disso, muitos sistemas eletrônicos permitem o registro e a análise dos dados de calibração, facilitando o monitoramento e a manutenção dos manômetros ao longo do tempo.
Outro método que merece destaque é a calibração em campo. Este método é utilizado quando não é prático ou viável transportar o manômetro para um laboratório de calibração. A calibração em campo envolve o uso de equipamentos portáteis que podem gerar pressões conhecidas e permitir a calibração do manômetro no local de instalação. Embora a calibração em campo seja conveniente, é importante garantir que as condições ambientais não afetem a precisão das medições.
Um aspecto importante a considerar na calibração de manômetros é a frequência de calibração. A frequência recomendada pode variar dependendo da aplicação, do tipo de manômetro e das condições de operação. Em geral, manômetros utilizados em aplicações críticas ou em ambientes severos devem ser calibrados com mais frequência do que aqueles em condições normais. É fundamental seguir as diretrizes do fabricante e as normas da indústria para garantir que os manômetros estejam sempre em conformidade e funcionando corretamente.
Além disso, a manutenção regular dos manômetros é essencial para garantir a precisão das medições. Isso inclui a verificação de vazamentos, a limpeza dos componentes e a inspeção visual para identificar sinais de desgaste ou danos. A calibração deve ser parte de um programa abrangente de manutenção que inclua inspeções regulares e ajustes conforme necessário.
Por fim, é importante ressaltar que a calibração de manômetros não se limita apenas à precisão das medições. A calibração de válvula de segurança, por exemplo, é um aspecto crítico que deve ser considerado em conjunto com a calibração de manômetros. As válvulas de segurança são projetadas para proteger sistemas contra pressões excessivas, e sua calibração deve ser realizada em conjunto com a calibração dos manômetros para garantir que ambos os dispositivos funcionem corretamente e em harmonia.
Em resumo, a calibração de manômetros é um processo vital que pode ser realizado por meio de diversos métodos, incluindo comparação com manômetros de referência, calibração por pressão de gás ou líquido, calibração eletrônica e calibração em campo. A escolha do método adequado depende das necessidades específicas da aplicação e das condições de operação. Manter um programa de calibração regular e realizar a manutenção adequada dos manômetros garantirá medições precisas e confiáveis, contribuindo para a segurança e eficiência das operações industriais.
Frequência Recomendada para Calibração de Manômetros
A calibração de manômetros é uma prática essencial para garantir a precisão e a confiabilidade das medições de pressão em diversos setores industriais. No entanto, a eficácia dessa calibração depende não apenas da qualidade do processo, mas também da frequência com que ela é realizada. A determinação da frequência recomendada para a calibração de manômetros é um aspecto crítico que pode impactar diretamente a segurança, a eficiência e a qualidade dos produtos finais.
Em geral, a frequência de calibração de manômetros pode variar dependendo de vários fatores, incluindo o tipo de manômetro, a aplicação específica, as condições de operação e as diretrizes do fabricante. A seguir, discutiremos esses fatores em mais detalhes, ajudando a entender como determinar a frequência ideal de calibração para diferentes situações.
Um dos principais fatores a considerar é o tipo de manômetro. Manômetros analógicos e digitais podem ter diferentes requisitos de calibração. Os manômetros analógicos, por exemplo, podem ser mais suscetíveis a desgastes mecânicos e, portanto, podem exigir calibrações mais frequentes. Já os manômetros digitais, que geralmente possuem componentes eletrônicos mais robustos, podem ter uma frequência de calibração mais espaçada. No entanto, isso não significa que os manômetros digitais não necessitem de calibração regular; a precisão dos sensores eletrônicos também pode ser afetada por fatores ambientais e operacionais.
Outro aspecto importante é a aplicação do manômetro. Manômetros utilizados em aplicações críticas, como na indústria farmacêutica, alimentícia ou petroquímica, devem ser calibrados com mais frequência devido à necessidade de conformidade com normas rigorosas de qualidade e segurança. Em ambientes onde a pressão é um parâmetro crítico para a produção, a calibração deve ser realizada em intervalos regulares para garantir que os instrumentos estejam sempre dentro das especificações. Por outro lado, manômetros utilizados em aplicações menos críticas podem ter uma frequência de calibração mais espaçada.
As condições de operação também desempenham um papel significativo na determinação da frequência de calibração. Manômetros expostos a condições severas, como altas temperaturas, umidade, vibrações ou produtos químicos corrosivos, podem sofrer desgastes mais rapidamente e, portanto, devem ser calibrados com mais frequência. Em ambientes industriais onde as condições operacionais são variáveis, é recomendável realizar calibrações mais frequentes para garantir a precisão das medições.
Além disso, as diretrizes do fabricante devem ser sempre consideradas. Os fabricantes de manômetros geralmente fornecem recomendações específicas sobre a frequência de calibração com base em testes e experiências anteriores. Essas diretrizes são valiosas e devem ser seguidas para garantir que os instrumentos funcionem corretamente e atendam aos padrões de qualidade. Ignorar as recomendações do fabricante pode resultar em medições imprecisas e comprometer a segurança e a eficiência dos processos.
Uma prática comum em muitas indústrias é a implementação de um programa de calibração que inclui a definição de intervalos de calibração com base em análises de risco. Esse programa pode incluir a realização de calibrações em intervalos regulares, bem como a realização de calibrações adicionais após eventos significativos, como manutenção, reparos ou mudanças nas condições de operação. A análise de risco ajuda a identificar quais manômetros são mais críticos e, portanto, necessitam de calibrações mais frequentes.
Além disso, é importante realizar inspeções visuais regulares nos manômetros, independentemente da frequência de calibração. Verificar se há sinais de desgaste, danos ou vazamentos pode ajudar a identificar problemas antes que eles afetem a precisão das medições. Se um manômetro apresentar sinais de falha, é recomendável realizar a calibração imediatamente, independentemente do intervalo programado.
Outro ponto a ser considerado é a integração de tecnologias que podem facilitar a calibração e o monitoramento da precisão dos manômetros. Sistemas de monitoramento em tempo real podem alertar os operadores sobre desvios de pressão e a necessidade de calibração, permitindo uma abordagem mais proativa para a manutenção dos instrumentos. Essa tecnologia pode ser especialmente útil em ambientes industriais onde a precisão é crítica e as condições operacionais podem mudar rapidamente.
Por fim, a calibração de torquímetro é um exemplo de como a calibração de instrumentos de medição deve ser tratada de forma integrada. Assim como os manômetros, os torquímetros também têm suas próprias recomendações de calibração, e a frequência deve ser ajustada com base nas mesmas considerações discutidas anteriormente. A calibração de diferentes instrumentos de medição deve ser parte de um programa abrangente de manutenção que assegure a precisão e a confiabilidade de todos os dispositivos utilizados na operação.
Em resumo, a frequência recomendada para a calibração de manômetros deve ser determinada com base em uma combinação de fatores, incluindo o tipo de manômetro, a aplicação, as condições de operação e as diretrizes do fabricante. Implementar um programa de calibração eficaz, realizar inspeções regulares e utilizar tecnologias de monitoramento pode ajudar a garantir que os manômetros estejam sempre em conformidade e funcionando corretamente. A calibração regular não apenas assegura a precisão das medições, mas também contribui para a segurança e a eficiência das operações industriais.
Erros Comuns na Calibração de Manômetros e Como Evitá-los
A calibração de manômetros é um processo crítico para garantir a precisão e a confiabilidade das medições de pressão em diversas aplicações industriais. No entanto, existem vários erros comuns que podem ocorrer durante esse processo, comprometendo a eficácia da calibração e, consequentemente, a segurança e a eficiência das operações. Neste artigo, discutiremos os erros mais frequentes na calibração de manômetros e forneceremos dicas sobre como evitá-los.
Um dos erros mais comuns é a falta de um padrão de referência adequado. A calibração deve ser realizada em comparação com um manômetro de referência que tenha uma precisão conhecida e validada. Se o manômetro de referência não estiver calibrado corretamente ou não for adequado para a faixa de pressão do manômetro em teste, as medições resultantes podem ser imprecisas. Para evitar esse erro, é fundamental garantir que o manômetro de referência esteja sempre calibrado e que seja utilizado um padrão apropriado para a calibração do manômetro em questão.
Outro erro frequente é a não consideração das condições ambientais durante a calibração. Fatores como temperatura, umidade e vibrações podem afetar a precisão das medições. Por exemplo, se a calibração for realizada em um ambiente com temperaturas extremas, isso pode causar dilatações nos materiais do manômetro, resultando em leituras imprecisas. Para evitar esse problema, é importante realizar a calibração em um ambiente controlado, onde as condições possam ser monitoradas e mantidas dentro de limites aceitáveis.
A falta de manutenção regular dos manômetros também pode levar a erros na calibração. Manômetros que não são mantidos adequadamente podem apresentar desgastes, vazamentos ou danos que afetam sua precisão. É essencial realizar inspeções regulares e manutenções preventivas nos manômetros, garantindo que estejam em boas condições antes de serem calibrados. Isso inclui a verificação de conexões, a limpeza de componentes e a substituição de peças desgastadas.
Outro erro comum é a calibração em intervalos inadequados. A frequência de calibração deve ser determinada com base nas diretrizes do fabricante, nas condições de operação e na criticidade da aplicação. Se a calibração for realizada com muita frequência, pode resultar em custos desnecessários, enquanto calibrações realizadas com pouca frequência podem levar a medições imprecisas. Para evitar esse erro, é importante estabelecer um programa de calibração que considere todos esses fatores e que seja revisado regularmente.
A falta de treinamento adequado dos operadores que realizam a calibração é outro fator que pode contribuir para erros. A calibração de manômetros requer conhecimento técnico e habilidades específicas. Se os operadores não estiverem devidamente treinados, podem cometer erros durante o processo, como a aplicação incorreta de pressão ou a interpretação errada das leituras. Para evitar esse problema, é fundamental investir em treinamento contínuo para os operadores, garantindo que eles estejam atualizados sobre as melhores práticas e procedimentos de calibração.
Além disso, a não documentação adequada do processo de calibração pode levar a erros e confusões futuras. É importante registrar todas as informações relevantes durante a calibração, incluindo as condições ambientais, os padrões utilizados, as leituras obtidas e quaisquer ajustes realizados. A documentação adequada não apenas ajuda a garantir a rastreabilidade, mas também permite que os operadores revisem o histórico de calibração e identifiquem padrões ou problemas recorrentes. Para evitar erros, implemente um sistema de documentação que seja fácil de usar e acessível a todos os envolvidos no processo.
Outro erro que pode ocorrer é a calibração sem considerar a faixa de operação do manômetro. Cada manômetro tem uma faixa de pressão específica em que opera com precisão. Se a calibração for realizada fora dessa faixa, as medições podem não ser confiáveis. Para evitar esse erro, é importante sempre calibrar o manômetro dentro de sua faixa de operação especificada e garantir que as pressões aplicadas durante a calibração estejam dentro dos limites adequados.
Por fim, a falta de verificação pós-calibração é um erro que pode comprometer a eficácia do processo. Após a calibração, é essencial realizar testes para verificar se o manômetro está funcionando corretamente e se as medições estão dentro das especificações. Isso pode incluir a realização de medições em pontos de pressão conhecidos e a comparação com as leituras do manômetro. Para evitar esse erro, sempre implemente um procedimento de verificação pós-calibração que assegure que o manômetro esteja operando corretamente antes de ser colocado de volta em serviço.
Além de todos esses erros, é importante lembrar que a aferição de balanças e a calibração de manômetros são processos interligados. A precisão das medições em diferentes instrumentos de medição deve ser tratada de forma integrada, garantindo que todos os dispositivos utilizados na operação estejam calibrados e funcionando corretamente. Isso não apenas melhora a precisão das medições, mas também contribui para a segurança e a eficiência das operações industriais.
Em resumo, a calibração de manômetros é um processo que pode ser afetado por diversos erros comuns, incluindo a falta de um padrão de referência adequado, a não consideração das condições ambientais, a falta de manutenção regular, a calibração em intervalos inadequados, a falta de treinamento dos operadores, a não documentação adequada, a calibração fora da faixa de operação e a falta de verificação pós-calibração. Ao estar ciente desses erros e implementar medidas para evitá-los, as empresas podem garantir que seus manômetros estejam sempre calibrados corretamente, contribuindo para a segurança e a eficiência das operações.
Em conclusão, a calibração de manômetros é uma prática indispensável que assegura a precisão e a confiabilidade das medições em ambientes industriais e laboratoriais. Através da compreensão da importância da calibração, dos métodos adequados, da frequência recomendada e dos erros comuns a serem evitados, as empresas podem implementar processos eficazes que garantam a qualidade e a segurança de suas operações. Investir em calibração não apenas protege a integridade dos produtos e processos, mas também contribui para a eficiência operacional e a conformidade com normas regulatórias. Portanto, é essencial que as organizações adotem uma abordagem proativa em relação à calibração de manômetros, assegurando que seus instrumentos estejam sempre em condições ideais de funcionamento.